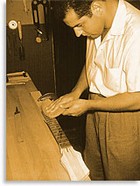
The story of Roger Rossmeisl’s career in the guitar industry had its roots with his father, Wenzel. Wenzel was born around 1900, Roger in 1927 in northern Germany, near the city of Kiel, about 50 miles from Denmark.
Wenzel was a professional jazz guitarist and a jazz guitarmaker. In the early 1930s, Wenzel made a trip to America and returned with a Gibson archtop jazz guitar. Guitars were as rare as guitarists in those days. Wenzel was inspired by the Gibson’s design and began to make his instruments with a similarly-arched top and back. He called them Roger guitars, after his son.
At some point the family moved, finally settling in Berlin just before the war. Berlin was an active city with a burgeoning love affair with jazz. This is where Wenzel hoped to make his living as a jazz guitarist and guitar maker. As the perils of World War II enveloped Germany, Wenzel stopped making guitars to take care of situation and family.
In the late 1930s, Wenzel sent young Roger away to school in Mittenwald, Southern Germany. Mittenwald is almost on the Austrian border near Garmish-Parkenkirchen, and is famous for its winter sports. Perhaps the most exquisite of Germany’s alpine villages, the brilliantly-painted town has an old world charm. Mittenwald also happened to be the home of one of the oldest and most famous violin and guitarmaking schools in the world, with a 300-year history of violin making. Today, the school still turns out master craftsmen. The added advantage of the school for the senior Rossmeisl was its remoteness from the coming war and safekeeping of his son, Roger.
Around the age of 10, Roger began his stay at the school as one of its youngest students. The school offered a full-range curriculum, from math and language to science and art, with a major emphasis on stringed-instrument making. The method of teaching in the school was one of master and apprentice. There was a strict attitude, and respect for the master was understood. For a time, Roger was responsible for getting up before everyone else to light the fire in the stove to heat the workroom. Located in the Alps, Mittenwald is very cold in the winter.
Skills were taught with the use of hand tools where modern-day crafters would use power tools. The workbenches for guitarmakers and violin makers were heavy, thick and solid. There were about four ways to clamp a workpiece in the bench. One of Roger’s masters was Franz Hirsch, a well-known guitar and lutemaker born in the 1800s. The table tops were occasionally scraped clean and flat, and Roger remembered Herr Hirsch coming around with a flatness gauge to check table tops. If the table top flatness did not measure up to Franz’s standards, students would have to scrape it again and again, until it was perfect.
The school believed in old-world classical traditions that translated into how instruments were made. Some students studied the making of violins, cellos and upright basses or bowed instruments, while others pursued the plucked instruments. The metric system was used exclusively for measurements. Some of Rogers specifications for the Fender acoustic guitars were metric 25 years later.
As the war raged on, Roger recalled that times got tougher; supplies diminished, tires were taken from vehicles, food was scarce and life got very serious. But he was safe, and life at school continued, intact.
Roger was at the school for some eight years and was one of the youngest graduates with a Masters Degree and title of “Gitarrenbaumeister” (Master Guitar Maker). The degree also gave him teaching credentials. He was then 18 years old. After graduation, Roger moved back to Berlin to work with his father and become part of the jazz scene.
By 1947, the senior Rossmeisl was producing his guitars and exhibiting at the Leipzig Fair. His guitars included an electric/acoustic Hawaiian guitar and a pickup for acoustic guitars. Wenzel may have been the first maker of electric guitars in Germany.
From drawings in “Die Gitarre Und Ihr Bau,” Wenzel’s Hawaiian guitar was probably a steel-stringed flat-top with a wide body at the 14th fret and the soundhole was more or less in the standard position. The string length would have been 58 to 66cm.
Wenzel also made the Roger guitar with some important design changes. Before the war, Wenzel’s jazz guitar archtop design was similar to the Gibson. Perhaps during his period of inactivity during the war, Wenzel had time to think and redesign his jazz guitar theory. Now the design was original and well thought-out. Wenzel began laminating as many as 12 pieces of wood together for the neck. The bridge was an asymmetric design, cross-drilled for lightness. The basic shape of the guitar was more-or-less standard. The carvings of the top and back were original and innovative, confined to an area about two inches from the edge of the body. Parallel to each other, with the idea that the entire flat area would move, thus moving more air for a bigger sound (much like a speaker flexes mostly at the outer diameter edge). This look came to be referred to as the German Carve. Later, Roger went on to use the look for his designs at Ricken backer, most notably in the Combo 800 and 600 from 1955 and 1957, to the more recent 381JK and the Fender LTD jazz guitar of the late ’60s.
About 1952, Roger became interested in going to America to work. He wrote to Ted McCarty, president of Gibson, and using his Gitarrenbaumeister diploma, received transport to the United States, and a job. During his first year with Gibson, he made an archtop jazz guitar that did not fit in with Gibson’s style. Conflicts arose and Roger left Gibson. He went on vacation and ended up in California, where he approached Rickenbacker in search of employment.
By 1953, Leo Fender’s Telecaster and Precision bass were picking up steam in the market. Francis Hall, the future owner of the Rickenbacker company (at the time, known as the Electro String Instrument Corporation), had established a radio repair business called Hall’s Radio Service, which became a wholesale electronic parts distribution company named The Radio and Television Equipment Company, set up in 1936 in Santa Ana, California, not too far from Leo Fender’s operation in Fullerton, California. Leo Fender became a customer of F.C. Hall’s for electronic parts.
By 1946, Leo was making lap steel guitars and amplifiers, and F.C. Hall became a distributor for Leo’s products. By 1953, the Telecaster and Precision bass were selling well and the sales arrangement between Hall and Fender was reorganized into the Fender Sales Company. The partners were Leo Fender, Francis Hall, and Charlie Hayes and Don Randall, both associates of Hall’s. Fender Sales became responsible for distributing all Fender products.
As the Telecaster, Precision bass and amplifiers gained popularity, Francis Hall became interested in the idea of manufacturing and distributing musical instruments. By late 1953, Hall learned of Adolph Rickenbacker’s interest in selling Electro String Instrument Corporation. He was able to purchase the company and the right to use the Rickenbacker name. The factory was being managed by Paul Barth, a long-time Rickenbacker manager. They were producing electric lap steel guitars and amplifiers. That was December of 1953.
In early 1954, Roger came to Rickenbacker and was hired by Barth. The timing was amazing, Leo just beginning with the Telecaster, and Rickenbacker about to design a whole new product line. Roger’s arrival, combined with the energy of F.C. Hall and Paul Barth, resulted in the introduction of Rickenbacker’s first contemporary electric guitars. The Combo 800 was a result of the combined efforts of Roger, Paul and F.C. Hall.
For the next eight years, Roger was largely responsible for the design of the majority of the Rickenbacker guitar product line.
In 1962, Roger went to work for Leo Fender, who brought Roger in to develop a new line of acoustic guitars. Roger found himself in a new facility on Missile Way in Fullerton, California, designing an assembly production plant for the new line. One day, early in the planning process, the receptionist brought in a job application of a young man named Philip, who was waiting in the front room. But that is another story.
Philip Kubicki (1944-2013) was one of the first employees hired by Roger Rossmeisl at Fender Musical Instrument’s R&D for acoustic guitars. He later founded Philip Kubicki Technology, building acoustic and custom electric instruments, as well as the Key Factor four and five-string basses.
This article originally appeared in VG‘s May ’97 issue. All copyrights are by the author and Vintage Guitar magazine. Unauthorized replication or use is strictly prohibited.